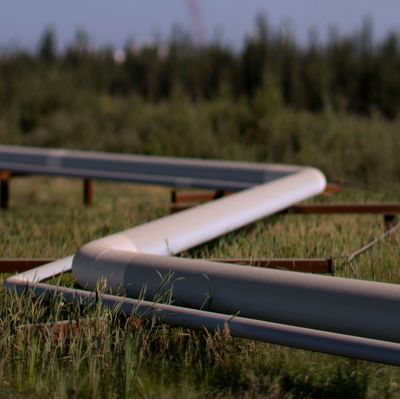
Darlene Gadson, 46
Production and Revenue Accountant
Bartlesville, Oklahoma
My job title at ConocoPhillips was production and revenue accountant. I tracked production for a gas plant in Canada — all of the gas and oil that came out of the ground and went through the pipelines to the processing plants. There were probably about 1,200 wells.
In the oil business, they talk about “upstream” and “downstream.” Things like machine fuel, heating oil for homes, and finished retail products like gasoline are considered downstream. I was “upstream,” which means closer to the point of extracting the raw material. The revenue side was accounting for all the revenue we had to pay to anyone who had an interest in the plant’s products, making sure they got paid when they’re sold.
In Canada, it’s not like you would find in the States, where you have individual owners of different wells. There are some individual owners, but the Crown or the government own a considerable portion of the mineral rights in Canada. You’re not going to see too many Jed Clampett scenarios. It’s going to belong to the Crown or to other large companies.
It was very expansive. There were thousands of miles of physical pipes. Thousands. Some of them were aboveground, some of them were below. The plant had two outlets just for gas after all of the natural-gas liquids had been removed, so we had two different pipelines that went to two different purchasers. We also had natural gas liquids or NGLs that were piped out, trucked out, or stored on site, depending on demand.
I did all this from our office in Bartlesville, Oklahoma. I went to Canada three times to tour the properties I was working with, but my production volume data all came from data-capture systems in the field. There’s a meter at the wellhead, where the product is coming out of the ground. They have other meters at various different points over the land, where they’re entering each new pipeline.
You have to analyze those meter readings and how that correlates back to each individual wellhead. If I felt there was a discrepancy, I had to communicate that, and people would physically go and look at a meter and see if it needed to be recalibrated. You needed to be very diligent to catch those discrepancies. If you didn’t, you had to go back later and do “an amendment.” You have to have people verify and double check. It could be another company gave you an incorrect volume and when they’re processing their amendment, you have to process one as well. The cost was about $20,000 for every amendment.
I had to track what percentage of the product was natural-gas liquids, what percentage was clean natural gas, condensate, and then track the pricing for each one. It’s different every month, different for NGL, different for gas. It depends on what time of the month it was sold. I would get my pricing from the marketing department in Canada. I just compile all of that data and send it to the department that does the paying.
I did not have any specific education or work experience before I joined ConocoPhillips. I didn’t start on that major gas plant. I started on a smaller property. I graduated to a little bit larger property. I went on to a little bit larger and then to the gas plant and I was there for four years.
A lot of the analysis is done on spreadsheets. You have to have a lot of complex formulas. That is the one area where I was seriously lacking. I had to really work hard to develop some Excel skills.
I learned when I was on the job by taking Excel classes they offered at ConocoPhillips. I also learned by what I would call reverse engineering. We have shared drives and I would look at spreadsheets other people had set up. I could look at their formulas and see what they were doing, and then I could extrapolate that.
I intentionally got an apartment that was two blocks from my office, so I walked. I typically put in at least a nine-hour day. The first few years, it was at least a 10, if not 12. Very challenging. But even though I would be at my desk for long periods of time, I didn’t feel like I had a ball and chain around my neck. There was a tunnel system underground between the buildings. I could go down there and walk for 10 or 15 minutes. I could go down to the cafeteria and get a specialty coffee. They also have ergonomics specialists, who come to your office, help you get fitted for the correct chair, help you get it in the right position, make sure your screen is the right distance from you.
I would honestly consider going back to work for them in the future. It’s a great company. Most people I knew stayed there as long as they possibly could and retired from there and they’d be very well off when they did. If I hadn’t had personal issues, I would have stayed there much longer. Working there, although it was highly stressful, it challenged me and I need to be challenged to be satisfied.
When I didn’t have the answers they provided me with more training or education to find those answers. They gave me the freedom to design and implement process improvement. They gave me the ability to train others, which I really enjoyed. The compensation and the benefits are phenomenal. The only downside was the stress level and the hours that were required. It was a lot of hours. I went multiple nights where I would wake up dreaming about work, about spreadsheets, about the well. It’s on your mind and in every fiber of your being. But I embraced that and I liked it. I would do it again for sure.
When I was there, my nickname was Rock Star. I covered for a co-worker once who was out sick for a few weeks. And then she decided not to come back for her own personal reasons. Since I had been covering for her, I talked to my manager, and I said, “How about I just absorb her work into mine? I’ve streamlined a process, I created desk documentation for it, step-by-step with screenshots, and I really think that I can tackle both as one individual.” That’s one way I got to be a top performer: I eliminated the need for a full-time position.
Sometimes we would go through some layoffs, and some co-workers I was friends with no longer had a job. It’s the nature of the industry. It’s a direct reflection of the prices you’re getting for oil, the prices that you’re getting for gas. On my floor there were about 120 people that did the Canadian accounting and there was about 11 or 12 that were let go. It wasn’t first in, first out. It really came down how they had performed and what kind of rating they had received. From talking to other people who worked there longer than I did, I got the impression the company does try to rehire those same people if they can.
My general attitude just from being in the industry is that I wish people were more mindful of the resources they’re using. People should ride bikes to work or walk more. Carpool whenever possible. Use more fuel-efficient modes of transportation. Try not to be wasteful of our natural resources and always keep in mind that they’re not limitless. We have to respect the environment and we have to respect those resources.
When I think environmentalist I think of people who go out to picket and stop pipelines. I would never go out and picket or strap myself to a tree or anything like that, but I do consider myself a minimalist by nature. I don’t have an overabundance of things. Every time something comes in the house, something goes out. I don’t like to use things to excess. I don’t like to be wasteful. I consider myself a conservationist. I do what I can in my own way to protect our resources.