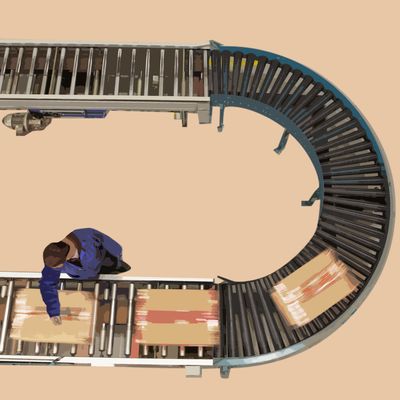
Russell Dow, 28
Shipping Expediter
Covington, WA
I chose to work at a warehouse when I turned 18, because I didn’t have any particularly useful skills, and it was easy to get a job. I wasn’t really drawn to it, but I didn’t want to do fast food or serving or anything.
Expeditors International has air import and export warehouses in just about every major city in the world which has an airport. I worked with a small team in the warehouse. We had about 12,000 square feet of floor space. We handled freight from companies in the Pacific Northwest, usually from within a couple hundred miles. There were companies like Flow which were down the street, and HySecurity which was about a mile away. Many others, like Micron, came from cities nearby, like Seattle or Kirkland. Philips Ultrasound came from Bothell. Kaiser shipped from Spokane.
Some shippers, like Micron, generally shipped to one country more often than others (Seoul, Korea). Ultrasounds, on the other hand, went everywhere. Practically every major city in Europe, Asia, Australia, Africa (mostly just Johannesburg), North and South America received ultrasounds. Where there are hospitals there are Philips Ultrasounds.
I got there at 5 p.m. When I arrived, I would shout out to my team, say hello, and let them know I’m there.
I’d usually start helping people on the doors. Truck drivers would come with freight, we’d check them in with fingerprint readers, get their picture and all the info about what they were bringing. As soon as we got the freight in the door we’d weigh it, take the dimensions, set it somewhere we could get to it easily.
The freight all needed to be labeled. We had to fill out forms saying who shipped it, where it was from, which freight was going to which country. We called this “dimming” the freight. Like for example, “Hey, can you dim the Spacelabs and put it on my desk?” Or “Mike needs us to dim and enter the Micron for the Seoul consolidation, so keep an eye out for it.” So I’d talk to whoever was doing that, figure out if they needed help.
In air freight, the name of the game is speed. People ship freight through the air to get it to its destination quickly. Attention to detail was crucial when you were labeling freight. Any mistakes could result in loss of product. Wrongly ship something to Brazil, and they might confiscate it. Mistakenly ship to Hong Kong, and they might destroy it outright.
A few years after September 11th, the TSA mandated that any freight going on a passenger flight would have to be screened for explosives. There was a lot of training for the screening process. You had to pass a lot of tests to tell you how to screen freight, how to use the machines to make sure they were working correctly. One-hundred percent of freight that we were booking on a passenger flight is checked. Every little box. If we had a shipment with 500 four-inch x six-inch x five-inch boxes, we’d screen every single one of them.
So I had a guy who’d start working the explosives-screening machine as soon as I got there. He would either have boxes along rollers that he would swab and detect, or he would swab larger “D-containers” — large boxes and crates not easily opened and detect on those.
Then we’d have another guy setting up what we call cookie sheets. After screening the freight, we put it on these gigantic rectangular pans, varying in size around 12 feet x 6 feet x 4–6 inches. We’d put it on these pans, wrap it in shrink wrap, and then throw a net over it. So you can put a bunch of freight on one, ship off to the airport and they’ll put it in the aircraft. Some airlines require this. They don’t pull it apart at the airport to do a second screen on it. If we said it was good to go, we’d send it to the airport and they’d put it on a plane.
Generally, what I would do after I figured out what everyone was doing and made sure no one really need a lot of help is I would start going through the computer and checking out what freight was going out for the day. I would look at the outbound list and try and get in my head, Okay, where are we sending most of our shipments to, what are we going to prioritize, how big are they?
So if everything was shipping to China, I would know, Okay, well we only ship to, like, three different ports in China, so these things are all going to need to be put together. By looking at its weight, and by knowing the names and style of the freight, I would determine how many trucks, of what size, I would need to order for the night to ship our consolidations up to the airport.
As soon as I had an idea of what we were looking at for the evening, I’d call one of our trucking companies, ask them to bring empty trucks of certain sizes, and tell them what time I needed them. Sometimes I’d order special trucks with a roller bed built in so that cookie sheets could be easily off-loaded.
We didn’t have racks like a lot of warehouses, because all our freight was in and out within the week, usually. We just staged it in rows based on the destination country, with the goal that most of the freight going to Hong Kong, for example, would be in the same row.
As soon as all the consolidations for one particular airline were labeled and ready, we would load them into trucks and send them to the airport.
This was the most stressful part of the day, because airlines have strict deadlines. If we don’t get the consolidation up to the airport within the cut time, our freight comes back to our warehouse, gets delayed a day, and we potentially have unhappy customers.
It’s a cyclical business. The busiest time of every year was always at the end of every quarter, so every three months it would usually pick up. Companies want to make sure their numbers look good for the previous quarter. We might have a company like Spacelabs, who wants to ship all their freight to our warehouse as soon as they could before the year ended, regardless of whether or not it actually shipped, so they could sign off and say, “Yes, we completed the shipment.” I usually worked eight to ten hours, but at the end of most quarters, and especially near the end of the year, I could be working 12-to-14-hour days pretty regularly.
When it got real busy, the warehouse would get so full that it was like a rat maze. The amount of freight in the warehouse can become constricting and claustrophobic. Just trying to maneuver anything was a huge pain. The one thing you needed was in the very back of the row. You’d move ten things to get to the one, you’d pull it out, and by moving those ten things, you bury the one thing you need 30 minutes later.
With all that freight, it gets hard to communicate with your team. You can’t even see them sometimes because stuff’s stacked up everywhere. If people are in a bad mood, it can get real bad, real ugly. I’m trying to direct traffic and get people to do one thing after another, and people are losing track of what they need to focus on next. They’re forgetting the things they need, I’m forgetting the things I need, the operations team is telling us they need one thing and we don’t have it.
When we lose focus we may screen things in the wrong order, delaying consolidations, or we might stage something behind a bunch of stuff that won’t be moving only to have to dig it back out again. We get a piece of freight and maybe we didn’t count boxes correctly, or mislabeled something, and it sits in our warehouse and we don’t even know it’s there. And it could be something crucial. In a worst-case scenario, people might be tempted to skip weighing freight (taking the truck bill estimation) or fudge the dimensions, which could result in major repercussions, and even loss of freight.
On a good day, I’d get there, I’m on time, the freight’s on time, everybody’s in a good mood, the airline labels come out early from the office, and I’m able to just pull everything out. We’d have a chance to sit down and chat with our regular truck drivers and not worry too much about stressing out about the airline cut times.
We’d have cool things that come in. We had pieces of an assembly line for Frito-Lay. We had a submarine come by one day, like a research sub. I think some of the most interesting freight we got were Gibson guitars. We did a lot of Gibsons.
In either case, good or bad night, at the end of it, when we’ve pushed out all we can get to the airport in time, we get to relax a bit and start taking lunch breaks. The intensity dies down, and sometimes we turn on the stereo. When the nights are really long and we’re preparing any freight we couldn’t get out for the morning or weekend, people sometimes get tired and a bit loopy and might start singing or being obnoxious with the forklift horns, like they’re trying to speak in Morse code or something.
Right before I quit, or about six months before, I got Employee of the Month. I felt really guilty because they were awarding me and I felt like they believed in me but I didn’t really want to be there. I’d decided, I don’t want to be here anymore. Physically, my job hurt me by being hard on my body, my knees in particular, my feet as well. It’s rough on the body to drive a forklift with poor suspension, it’s horrible to run and walk on cement in stiff protective shoes all day.
I was absolutely grateful for my job. It was steady, I made decent money. I loved working with the wide array of people I met. I was making $13 an hour when they first hired me. I think I worked there a total of six years and I was only up to $15.75. I wouldn’t call it a good-paying job, but for someone young and energetic it’s not really bad.
I loved being a leader, having people look up to me and ask me for direction. I loved having a broad understanding of what we were doing, being involved in decision making, I loved communicating with co-workers, customers, and vendors. Developing relationships with people is what made it all worth it. I think that’s the case in anything that you do.
I’m not sure there is anything I am ever “meant” to be doing, or anyone, for that matter.
Today, what I really want to do is start a career as a software developer. A friend of mine had started the computer-science program at Remy Tech, and he was like, “Hey, I know you like computers. This is something you’d be interested in. Trust me.” So I was like, “Whatever, I’ll try it. Let’s see what happens.”
I fell in love with it. I LOVE it. It’s amazing. It was so much fun to write some code and then see it actually do something on the computer. I have one more class to complete and then I have one year left of my bachelor’s degree.
I grew up in a poor family, but I feel like we live in a privileged world. In America, “poor” isn’t comparable to “poor” in another country like India or Sudan or something. If you are born in a first-world country, you have all the reason to believe you can do whatever you want. Especially with the number of resources available today, there are very few reasons anyone can legitimately claim to hold them back from achieving the things they want.