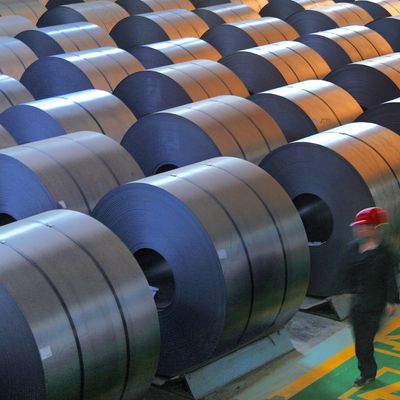
Jeanie Koval, 56
Steel-mill worker
Burns Harbor, Indiana
I work at ArcelorMittal in Burns Harbor, Indiana, just due east of Gary. I’ve been working here for 38 years at the end of this month. I was hired into the cold mill — when we were Bethlehem Steel, it was called the cold mill, but the name got changed to the finishing mill later on down the line.
I didn’t really aspire to be a steelworker. I came here when I was just on the verge of being 19 years old. My husband went off to school and that was really hard, being a young adult and missing my boyfriend. At that point I couldn’t decide if I wanted to go to college or if I was just taking some time off. I came for the application-day and got the job. I said, Oh, I’m going to work here for two years and save my money; then I’ll figure out what I’m going to do. Here I am 38 years later, because life happens. Listening to my friends who graduated from college, now they can’t find jobs or at least find a good-paying job. I was making more money than they were — and that’s still the case.
Molten steel gets poured into these forms that turn them into the big slabs. Then from there they go through the plate mill, where the plate mill will hammer them down into thinner material and from there, I don’t know exactly where it goes — to something like the hot mill that will bring the gauge down even more, into a coil.
The coils vary in sizes. Small coils run 20,000 pounds. The heaviest coil we have is probably 65,000 to 70,000 pounds. Then it comes into the finishing mill, which is where I work. It goes through a process; it depends on what type of steel that is ordered. Somebody might want a softer steel that is bendable, where it goes into a stamping plant for a vehicle where they can mold it. Or it could be a very hardened steel that doesn’t mold easily. They would use that for steel drums for chemicals or oils.
The shipping department is the last stop before the coils go out the door to the manufacturers. We produce most of the steel for the automotive industry. We also see a lot of trains going to Mexico. We package and ship them. They get transferred with forklifts and big tractors. The crane puts them on a truck or a train.
If you can imagine, the coils come down on a conveyor, they’re on a track that travels from point A to point B in a straight line, without stopping, down through the warehouse until they reach the crane. Then the crane picks them up and delivers them to the shipping department for us to package. Or, if they’re already packaged because they got banded at the mill, they go right into the warehouse to be stocked and then manifested.
I work in the loading department now. We load the coils out on railcars or ship them out on trucks. We usually put four to five coils on a railcar. It’s a physical job in the respect that you are pulling the bulkheads, which are 15-inch-wide plate-spacers that are in between the coils. They have chains on each end of them and there’ll be one person on each side of the railcar and they’ll pull the bulkhead to the coil to secure it on the railcar. If we’re not loading railcars, we’re loading trucks and they’re being put on there by the crane. All I do with that is to check to make sure it’s the proper coil. We’re pretty automated now. We have a kiosk and an RFID reader. If it’s not working then that’s where I am to fill in the gap.
Most of my career I have been in the shipping department, banding or wrapping coils. My friend used to say I was a gift wrapper. I don’t mind my job. I’ve been here for so long that it’s second nature to me. In the summer, it’s extremely hot because there’s not a lot of airflow in the building and it’s not climate controlled. It’s a warehouse, so you can imagine the sun beating down on the building. In the winter it’s extremely cold because we don’t have a lot of heat.
Once you do something for so long you get a pace going. I’m used to it. To me my job is like a workout. It’s physical. When we don’t have any coils, we take a break until more coils come. They don’t stop, that’s for sure. They just keep coming.
My father was a steelworker. He worked at U.S. Steel, in Gary. I had an aunt who worked in the steel mills, too. She was older than my dad. She worked at the metallurgical lab, testing the steel to make sure all of the properties were correct. If she were here today, I’m sure we could have some conversations about what it’s like to be a woman working in a steel mill.
I grew up in Gary. I have classmates who I work with. There’s a lot of people here that I hired in with in 1979. Never in a million did I think I’d be working for 38 years. I thought I was going to retire with 30 years.
In the early 2000s, Bethelehem Steel went bankrupt, but we didn’t lose our jobs. Wilbur Ross saved the mill. That was a great feeling because we were worried that the bankruptcy was going to close the doors. A lot of people would have lost their jobs and this area really depends on the steel mills to support all of the businesses around here. It was a good feeling because we knew that there was some hope then.
When Bethlehem Steel filed for bankruptcy, that changed everything for everybody. They offered a buyout. A lot of people took the buyout, mostly people that had 30 years or more. They also offered to pay for you to go to college and get a degree as part of their severance package. One of my co-workers took the buyout, he was in his late 40s, and he went to school and he was on the dean’s list. But even today, he wishes he had his job back. He’s not making as much money as he made in the steel mill. He regrets it. The job he has now doesn’t offer him as good health insurance and pension.
When they went bankrupt, if you had less than 30 years, you lost two-thirds of your pension. I had 24 years at the time. Oh my goodness, it was devastating. It just gives you a sinking feeling that all of the hard work that you devoted to this company is not being rewarded at the end like you thought that you were. It gives you a pit in your stomach. You have to rethink your game plan about retirement.
So I’m working on a whole new pension.
Most steelworkers are Democrats. But it’s actually a topic of conflict because a lot of people voted for Donald Trump. He said that he wants to bring all of the jobs back to America. We want to try to keep all the steel in America and stop the steel from coming in from other countries. That’s always going to be an issue. People wanted change. A lot of young people didn’t really understand Hillary’s vision and when they heard Donald Trump say that he wanted to bring jobs back to America and keep the steel industry intact, that really piqued their interest.
I would say people were 50-50. I’m trying to give him a chance. I’ll have to assess his goals as times goes on. But I’m not a big fan of Donald Trump. He’s a businessman, not a politician. He doesn’t have very good manners, that’s for sure.
The union means everything to us. The union negotiates our wages and our benefits, and our benefits package is huge. Our package for our benefits is probably the same as it is for our wages. So we have medical insurance, sickness and accident pay, prescription benefits, vacation pay, retirement benefits. All of that stuff is negotiated with the company through the union. We have job protection and a safety team that’s also negotiated in our contract. Safety is big. It’s very important. Last year I think we had the least amount of lost work days as we’ve ever had.
Every job has its hazards, but a steelworker has a lot of hazards. You’re putting your life at risk when you walk through the door. You have to wear your hard hat, your steel-toed boots, your safety glasses, and long sleeves and pants. We have a lot of hazards, such as slipping and tripping. You always have to be aware of your surroundings because there’s overhead cranes and forklifts and big steel-hauling tractors or big tractors that pull buggies with six coils on them. You have to be very careful of everything, even the steel itself. You can get cut on the steel.
The very first accident that I actually witnessed was last year. I was banding coils off of a production line with this gentleman, a very tall lanky guy. We started to band the coil but the conveyor was moving and he accidently had his foot underneath the coil. The conveyor was actually moving over his foot. It’s not a good practice to band the coils with the conveyor moving, but it moves at a really slow pace so we do it in order to get the coil banded before the next coil comes off. Like I said, they don’t stop. As it was happening, he was saying to me, “Jeanie, the conveyor is running over my foot.” I thought he was kidding, I was like, ‘no, it’s not,’ and he said, ‘yes, it is,’ and I could tell by his eyes that it was.
So I hit the emergency stop and, thank goodness, he didn’t get hurt. His boot saved his foot. He got lucky. He was shaken up. He couldn’t move. His foot was wedged. There’s not very much clearance between the coil and the floor plate. We had to call 911 and we all went into action trying to help him. The electricians had to come and reverse the conveyor. It was a pretty dramatic scene for a minute there. I don’t want to be a part of that again.
I would want anybody’s children to work in a steel mill. They’re good jobs. Good-paying jobs. Good benefits. My father raised a family of five girls on a steelworker’s wage. My husband and I worked hard to get our daughters through college and get them on their own, and I think we did a good job doing that.
The lake means everything to me. I live to go to the beach. Where I live, in Gary, it’s just a block away from my house. When I look to the west, I see U.S. Steel and I’m reminded of my father and aunt and uncle who all worked there. When I look to the east, I can see where I work. Now that we’re planning for retirement, we’re getting ready to build a house that we can retire in that’s a little bit closer to the beach than we are now. I’ll be about 100 steps away.